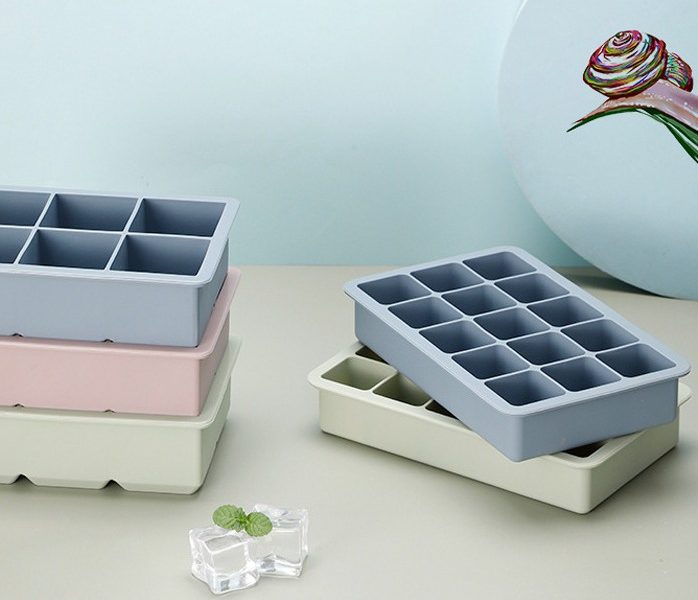
The process of custom silicone products is more complicated, and it is more important for you to confirm the details before production.
If you are a buyer or a brand owner of silicone series or an Amazon e-commerce seller, you need to purchase silicone products in large quantities or custom silicone product brand. It is also important to choose the right silicone manufacturer, including production and R&D capabilities, price, and service. Ability etc.
You need to clearly know the following steps to ensure the quality of your products. The following tips are very important.
1. Determination of drawings and designs
Does the project you need have 3D drawings of the molding?
If so, it can be sent directly to the manufacturer for confirmation of details and quotation. If there is no drawing or you only have an idea, you need to have in-depth docking with us and we will help you. design,
Of course, if you have samples, just mail them to us directly, and we will directly start mold production based on your samples, which will save more time and effort.
2. Sample design and determination:
After confirming the drawings, we will follow the drawings to open the mold and need to connect with you. This is very important. For the determination of the sample:
1). Silicone material:
Both parties need to confirm the usage scenario of the product. Whether your product is medical grade, food grade or industrial use. If it is a custom silicone product for pets or babies, you need to confirm that the silicone material is food grade. , and the silicone manufacturer is required to issue corresponding certificates, such as FDA or LFGB, etc.
Choice of liquid silicone or solid silicone: Liquid silicone: Liquid silicone is suitable for making complex parts and molds, able to completely fill in fine details. It is often used for products with complex shapes or requiring high precision.
Suitable for processes such as injection molding or vacuum casting, ensuring that liquid silicone fills all gaps in the model.
Solid silicone: Solid silicone is suitable for simple molds or products requiring higher hardness and strength. It is usually used to make seals, gaskets, etc. with higher hardness.
It is suitable for extrusion molding, calendering molding and other processes to ensure that the silicone can maintain the required shape.
The choice of liquid or solid silicone depends on the shape and hardness requirements of the product and the requirements of the production process.
2) Hardness of silicone
Silicone material is a relatively soft green material. You need to determine the hardness according to the object and function of your product, so that we can produce the most suitable raw material hardness during the rubber mixing and preparation process. The greater the hardness number. , the harder the product is, for example, a silicone dog bowl, it is generally recommended that the hardness is about 70, and the hardness of the silicone placemat should be correspondingly lower, so that it can be folded and stored easily after use by consumers.
3) Color:
Determine the color of your custom silicone product, whether it is a single color or a mixed color. After the sample arrives, make sure there is no color difference. If so, you need to communicate with the silicone manufacturer and re-adjust the color until it reaches the corresponding standard. Appearance: Make sure your appearance is consistent, whether you need to add a logo, etc.
4) Smoothness:
Whether there are burrs on the surface of the product, whether it is smooth or the surface of the product can be polished according to your requirements
5) Whether it fades
If some products need to be sterilized and placed in a microwave or dishwasher, you need to actually test whether the color will fade after use.
6) Rebound effect:
Silicone material is very suitable for manufacturing silicone folding cups. If your product is a foldable silicone cup, you also need to test the rebound speed of the gas product. If the rebound speed is inconsistent, it will also affect the consumer experience.
7) more details
If your product is a silicone tube or other product that needs to hold liquids, sealing is also very important.
There are more details and important matters if your product has more
1. If you also need other projects, such as outer packaging and in-depth development and customization of brand tone, the following factors also need to be considered by you:
1) Cartons: Eco-friendly, durable and available in a variety of shapes, sizes and finishes to meet your brand and product needs
2) Printed Labels: High-quality adhesive and non-adhesive labels with eye-catching designs that convey your brand image
3) Hang Tags: Unique, eye-catching hang tags that convey important product information and reinforce your brand image
4) Barcode Stickers: Customizable barcode stickers for efficient tracking and inventory management.
5) Customized Bags: Personalized bags in a variety of materials, sizes and styles, from reusable totes to luxury drawstring bags.
2. Mass production of silicone products
After the sample is confirmed, the large-scale mass production phase begins. You need to determine what kind of silicon manufacturing process is required based on the characteristics of the product.
Different silicon manufacturing processes will have different efficiencies and production costs. Generally, as a professional top-level custom silicone products manufacturer, we will choose the appropriate manufacturing method based on the characteristics of your product:
Silicone Injection Molding
Features: Silicone injection molding is to inject pre-heated and melted silicone into the mold, and manufacture silicone products through high-pressure injection molding. This method is suitable for producing larger batches of silicone products, and has high production efficiency and precision.
Scope of application: Injection molding is suitable for the production of silicone products with complex shapes, precise dimensions and high-quality requirements, such as medical devices, auto parts, industrial seals, etc. The mold cost of this process will be relatively expensive
Silicone Compression Molding
Features: Silicone compression molding is to place pre-heated silicone in the mold, and then use a press to press the mold into shape. Compared with injection molding, this method has lower equipment cost and is suitable for the production of small and medium batches of silicone products. This is the most common processing method
Scope of application: Compression molding is suitable for the manufacture of silicone products with simple shapes and relatively large sizes, such as silicone seals, household items, toys, and baby products.
Silicone Extrusion Molding
Features: Silicone extrusion molding is to extrude pre-heated and melted silicone through an extruder to produce continuous silicone products, such as silicone tubes, silicone strips, etc.
Scope of application: Extrusion molding is suitable for producing long strips of silicone products with the same cross-sectional shape, such as sealing strips, pipes, hoses, etc. This mode of production yields relatively high yields.
Silicone Double Shot Injection Molding
(Silicone Over Molding or Silicone Multi Shot Injection Molding)
Features: Double-shot injection molding is to inject silicone on the surface of another material (usually plastic) in one molding process to form a composite silicone product.
Scope of application: Two-shot injection molding is suitable for the manufacture of products with silicone properties, such as soft, high-temperature-resistant surface coverings, handles, etc.
Silicone Clean Room Injection Molding
Features: Clean room injection molding is to perform silicone injection molding in a high-clean production environment to ensure high purity and cleanliness of the product.
Scope of application: clean room injection molding is suitable for medical, food and other fields that require high product cleanliness and purity, and has relatively high requirements for the production workshop environment.
Logo customization:
Determine the usage characteristics of your product and choose the most reasonable logo customization method. We can provide the following 10 or so silicone product logo customization solutions:
1) Concave and convex engraving:
During the processing of silicone product molds, the LOGO position is reserved by making the mold, and the LOGO pattern is milled at the corresponding position. The silicone raw material is placed in the silicone mold, and the silicone is vulcanized at high temperature. Finally, Get the finished silicone product with LOGO.
2) Silk screen printing:
Silk screen printing is a relatively mature printing technology in the silicone printing industry. The pattern printed in this way has a strong three-dimensional effect and will basically not fall off after printing is completed. Currently, the clarity of the screen printing screen in the industry can be very high. Precision.
3) Pad printing:
The pad printing process uses a concave engraved LOGO pattern on a steel plate, and uses a rubber head as a carrier to print the pattern on the silicone product. It is often used for printing irregular patterns on silicone products.
4) Color printing:
The color printing process is ink printing equipment that prints silicone ink on silicone products, and a chemical reaction occurs between the ink and silicone. Usually this type of printing process requires the silicone background color to be white, and secondly, the printing workshop must be done during printing. Dust-free, otherwise particle dust will be generated on the LOGO or pattern after printing.
5) Transfer printing:
Transfer printing is to pre-print the pattern on the transfer film, and transfer the pattern to the surface of the silicone product through thermal transfer equipment. After molding, the ink and silicone are integrated.
6) Laser engraving:
The laser engraving process is a LOGO pattern production method that sprays black light-shielding touch oil on the silicone surface, and then engraves the LOGO pattern through laser. It is usually used in the buttons of some electronic and electrical equipment with light-transmitting effects. More extensive.
In addition to the above printing processes, there are many other methods for printing silicone products, such as surface glue dispensing, UV transfer printing, water transfer printing and other printing processes. After silicone products are printed, the product patterns are rich in layers, the colors are bright and not easy to fade, have rich three-dimensionality and gloss, and have certain anti-slip effects.
Custom silicone products production is completed, and your final delivery date and logistics method are finally confirmed, so that your customized silicone product project is basically completed. Finally, I wish you a prosperous business and everyone!
Our product collection: https://www.growsilicone.com/product-collection/
You can purchase directly from our product range or find inspiration in our product collection to custom silicone products to grow your business, we are your best partner in business!
If you need custom silicone products, contact Growsilicone: