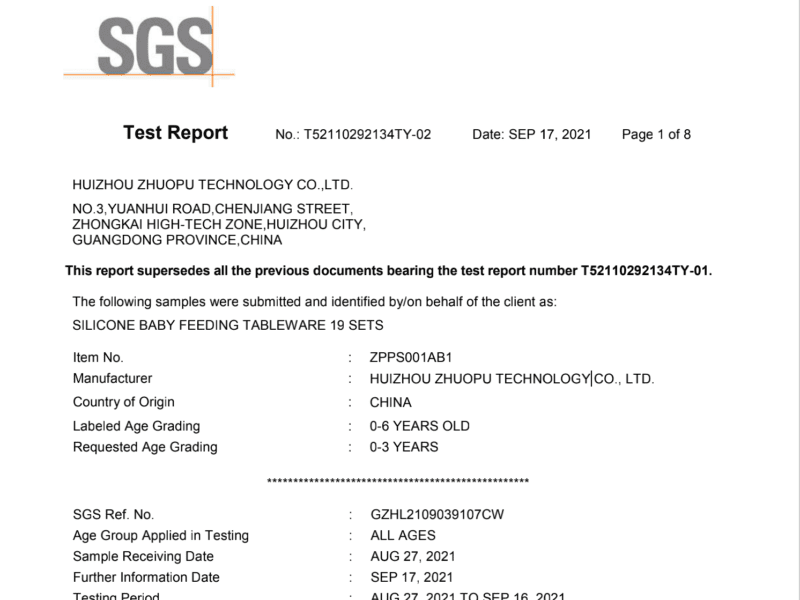
Customized silicone products factory require professional industry certification, and the certification standards and certificates for silicone factories vary depending on the type of silicone used.
China: CCC, SRRC, CQC, GB quality inspection reports.
EU CE, RoHS, ERP, REACH, GS, WEEE, LFGB, etc
North America: FCC, FDA, CEC, UL, ETL, IC, CSA, EPA, and other certifications.
Japan: PSE, TELEC, VCCI
Korea KC, MSIP
Australia: C-TICK, RCM, SAA, MEPS
Saudi SASO, Nigeria SONCAP, Kenya PVOC, etc
Inspection standards for custom silicone products
- General standards
- 2. Working temperature: -15 ℃ -+80 ℃
- Storage temperature: -30C -+85 ℃
- Storage time: Product A can be stored for a long time when placed flat without compression
- Storage of products under compression: 1 month
Working relative humidity: 45% -95%
Working pressure: 86-106Kpa
Contact rate: 5MA at 12VDC/0.5 seconds/2 * 107 times
contact rebound<12 milliseconds
Insulation resistance>1012 ohms/500VDC
Breakdown voltage:>25KV/mm
2、 Appearance
1. Color
(1) There is no significant difference in the exposure of silicone after standard vulcanization assembly
(2) Test method: Under bright natural light or 40W fluorescent lamp, place the standard sample or color card with the sample to be calibrated
Together, professional personnel with visual acuity of 10 or above and no color blindness are required to observe a distance of 30cm between the naked eye and the sample
Visually inspect for 5 seconds under normal conditions
- Eccentricity
(1) Standard: When the thickness of H-thick – H-thin elastic wall is ≤ 0.1MM, during mold inspection
X=20%;
When the elastic wall thickness is ≤ 02MM, X=15% during mold inspection
When the thickness of H thick+H thin elastic wall is ≤ 03MM, X=8% during mold inspection
(2) Testing method: Use a thickness gauge for testing.
3.Overflow
(1) Standard: From key down
It is recommended that the height of the monochrome material ≥ the height of the exposed shell+1.0MM and cannot be seen after installing the shell
(2) Test method: measure with Vernier scale
- Burr edge
(1) Standard product edge: ≤ 0.5MM
Positioning hole: ≤ 0.1MM
- Rupture
(1) Where the standard does not affect assembly and usage performance: ≤ 1.0MM
(2) Test method: measure with Vernier scale
- Color dots, concave and convex dots
(1) Standard customer assembled silicone exposed parts: no obvious visible
Testing method: Place the sample under bright natural light or a 40 watt fluorescent lamp
At a distance of about 30cm from the naked eye
Visual inspection for 5 seconds for individuals with vision above 1.0
- Character offset above
(1) Standard center value ± 0.15MM
(2) Detection method: Measure with a tool microscope
3、 Physical performance
- Size
L<10: L ± 0.05MM
10 ≤ L<20: L ± 0.08MM
20 ≤ L<30: L ± 0.10MM
30 ≤ L<50: L ± 0.15MM
50 ≤ L<100: L+0.3% LMM
100 ≤ L: L ± 0.5% LMM
(2) Detection method: Measure with a projector
- Elasticity
(1) Standard:
- Peak P1
Standard value: 50 ± (5-10) g
70 ± (10-15) g
90 ± (15-20) g
100 ± (15-20) g
120 ± (20-25) g
150 ± (20-25) g
170 ± (25-30) g200-300g ± 35g
Minimum rebound P3
When P1 ≤ 50G: P3 ≥ 20G
When 50G<P1 ≤ 120G: P3 ≥ 25G
When 120G<P1 ≤ 180G: P3 ≥ 30G
When 180G<P1 ≤ 250G: P3 ≥ 40G
When 250G<P1: P3 ≥ 50G
Feeling: 20% -80%
Discreteness
When the center value of P1 is ≤ 150g, the same key type of the same product in the same piece is ≤ 15%
Same key type for different chip products: ≤ 20%
When the P1 center value is ≥ 150g, the same key type of the same product in the same piece: ≤ 20%
Same key type for different chip products: ≤ 25%
(2) Test method: Use the AIKOH MODEL1305 elasticity measuring instrument to measure the variation curve of elasticity with stroke. Read its peak value P1, contact elasticity P2, and minimum rebound P3. Calculate its:
Feeling=(P1-P2)/P1 * 100%
Discreteness=(P1 max peak) – P1 (min peak))/P1 (max peak
Value) * 100%
- Contact resistance
(1) Standard:
Black particle conductivity ≤ 100 ohms
- Transfer printing conductivity: ≤ 250 ohms
C Screen printing conductivity: ≤ 500 ohms
(2) Test method: Use a pressure of 250g to compress the conductive base of the product key at intervals of
On a 0.5MM single slit half moon shaped gold-plated plate. After the multimeter displays a stable value, read the displayed value
- Service life
(1) Standard: 500000 times
(2) Test method: When the AIKOH silicone life tester has a strike rate of 2-5 times/second, set the strike contact stroke of the strike platform to product stroke+[0.1-0.2] mm. After 100000 strikes, the elastic wall should not crack, damage, and rebound, with a loss of ≤ 30%. When the customer does not require it, the test should be conducted at 500000 times
- Printing conductive life
(1) Standard: 2000 times
(2) Test method:
- Service life
(1) Standard: 500000 times
(2) Test method: When the AIKOH silicone life tester has a strike rate of 2-5 times/second, set the strike contact stroke of the strike platform to product stroke+[0.1-0.2] mm. After 100000 strikes, the elastic wall should not crack, damage, and rebound, with a loss of ≤ 30%. When the customer does not require it, the test should be conducted at 500000 times
- Printing conductive life
(1) Standard: 2000 times
(2) Test method: When the AIKOH silicone life tester has a strike rate of 2-5 times/second, set the strike contact stroke of the strike platform to product stroke+[0.1-0.2] mm. After 200000 strikes, the conductive substance must not detach from the conductive substrate and its contact resistance is within the specifications
- Printing font lifespan
(1) Standard: ≥ 100 turns
(2) Test method: Install the character single key on the PK-3-4 font lifespan tester, so that the key is higher
0.5-1.0MM, with 500G pressure rotating friction and continuous font opening, visual thickness method can be used for lifespan control when customers have no specific requirements
- PU lifespan
(2) Test method: Install the test KEY on the RCA friction tester and expose the height
When the font is damaged at a pressure of 0.5-1mm and 175g, the lifespan is the PU lifespan. If there are no customer requirements, the PU lifespan is based on this standard
4、 Chemical properties (limited to silicone buttons on recording phones)
- Heating weight loss rate
(1) Standard: a ≤ 0.2% (after weight loss after heating at 200 ℃/4HRS)
- ≤ 1.0% (after weight loss after heating at 200 ℃/24HRS)
(2) Test method: put the product in the drying oven for 30 minutes, then take it out, use the Analytical balance to weigh the weight W1 of the product before the test, put the product into an oven with a temperature of 200+/-5 ℃ to bake for 4 hours or 24 hours, then take the product out and put it in the drying oven for 30 minutes, use the Analytical balance to weigh its weight W2, and calculate the value of (W1-W2)/W1 * 100%
- Extraction weight loss rate
(1) Standard: ≤ 3.5%
(3) Test method: select some representative keys, cut about 0.5g of sample and then cut it into 0.005-0.01g of small particles, use the Analytical balance to weigh its accurate total weight as W1, put the sample into the extractor and add IPA for extraction for 2 hours, then take out the sample and put it into the temperature of
Bake in an oven at 00 ℃ for half an hour, take it out and cool it in a drying oven for half an hour. Weigh the accurate total weight W2 and calculate the value of (W1-W2)/W1 * 100%
- Low molecular content
(1) Standard: D3-D10 ≤ 300PPM
Test method: Select a representative 100+/-0002g sample of keys, cut it into small particles of approximately 2mm, and place it in
Pour 20MLCCL4 solution into a small bottle and add 20UL of it
Standard substance (CH3 (CH29CH3)
Shake well and store 16-24 HRS, measure the amount of D3-D10 using a chromatographic analyzer
GROW-SILICONE, we have a professional silicone products factory and we will provide genuine and professional product certification certificates according to customer requirements.